Interview with Lids Supplier, Termoplast
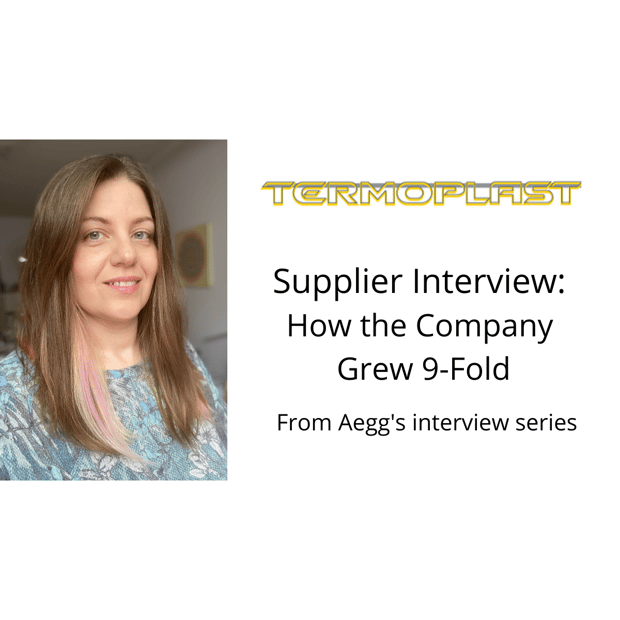
Aegg interviewed Zhana Ivanova, from Bulgarian packaging company Termoplast (and packaging lids supplier to Aegg), talking about growing 9-fold, recycling, the cost of raw materials and working in every division of the company…
1. Can you give a little background about Termoplast?
Termoplast was founded in 2001. We are a family based company and our factory is situated in Burgas, Bulgaria, a beautiful city on the Black Sea coast. My father Pesho Ivanov, is the CEO; my sister Elena Ivanova, is in charge of the design of the packages and all Bulgarian key accounts; and I am currently in charge of all administrative work and foreign accounts. We are working together to make all the processes run as smoothly as possible.
We have 3,500m² of production and storage areas and, at the end of 2021, we added a much needed expansion to our warehouse. Currently we thermoform PET, PS and PP sheets into more than 500 different packages for food. Production runs 24 hours a day, 350 days a year. А well equipped mould manufacturing unit gives us the advantage to design and produce custom made packages very fast and at a low cost.
Since we started working with Aegg 7 years ago, we have designed and produced a wide range of PET lids for their plastic and glass pots and bowls.
Since we started working with Aegg 7 years ago, we have designed and produced a wide range of PET lids for their plastic and glass pots and bowls.
2.What major changes have you seen since the company was formed?
We have expanded our output by more than 10 times
We have continued to grow over the years. We started with 10 employees and 1 thermoforming machine; now we have over 90 employees and 12 thermoforming machines. We have expanded our output by more than 10 times and we are continuing to grow. We also managed to close the production cycle: now we are extruding a third of the sheets we thermoform and we are reworking all of our scraps. Nothing goes to waste. We have expanded our output by more than 10 times
3. What are the future development plans at Termoplast?
We are looking to produce more PET and PP packaging and eventually to replace most PS packages with more widely recycled materials. We have a new addition to our machine range which is focused on thermoforming PET and PP. The next couple of years will be pivotal in introducing our current portfolio made from different materials.
4. How has business been impacted by the increased cost of raw materials and gas?
The constantly rising cost of raw materials has definitely had a big impact on our work. We had to increase the price several times, which we haven’t done since 2012. It is a very delicate matter because our long term clients were not prepared for it.
Since 2020 we installed a solar photovoltaic installation on the roof of our factory. In 2021 we extended it to 300kW. We are adjusting our manufacturing schedule for the most electricity consuming processes daily, depending on the weather and we are trying to get the most out of what the sun gives us. During the daytime in the summer we produce more energy than we can use. That gave us an idea and now we are researching possibilities to store energy in batteries so we can use it during the night.
5. What do you think sets Termoplast apart from your competitors?
"We have a lot of experience in developing custom made packaging"
We have а lot of experience in developing custom made packaging. Whether it is a lid, a small chocolate box blister or a large cake package, we can make it. Since we are making the moulds ourselves we can make them very fast.
Nowadays a lot of food producers are repacking their products because of the changing economy. The consumer wants a smaller net weight of product per package, or they want to buy in bulk. To answer the fragmented market, producers are forced to give consumers more options. We can offer them a new packaging solution fast and at a low cost.
The other advantage we can offer to our local market is flexible delivery provided by our own logistics.
6. How does sustainability play a part in your business?
Sustainability is a very important part. It is a balance between environment, equity and economy. It is about keeping our natural resources for our children, for our health and prosperity. When I started working in our family company Termoplast in 2009, plastic packaging was against my own principles and beliefs. So I started researching possible greener alternatives for plastic packaging. More than 10 years later I am still looking forward to finding them.
Only a small percentage of the world’s oil supply is used for making plastics. Plastics are durable yet lightweight, but more importantly, they can be recycled and that means no waste.
Plastics are durable yet lightweight, but more importantly, they can be recycled and that means no waste.
PET is the most widely recycled material suitable for food packaging so far. We will be switching a large number of or PS packaging to PET in the future. Currently 50% of the PET sheet we use is made from post-consumer recycled material. I definitely see us using 100% recycled PET in the future.
7. What key factors do you think will play a big part in the packaging industry during 2022 and beyond?
The expansion of recycling for all kinds of plastics is a key part of the future.
The expansion of recycling for all kinds of plastics is a key part of the future. We need plants for chemical recycling of plastics. Chemical recycling will give us the opportunity to use more post-consumer recycled resin in food packaging.
We should also not underestimate the part that consumers play in the process. People should be conscious about recycling and do their part so we can have a greener future. I am glad to see that every year more recycling campaigns and initiatives are taking place amongst the younger generation.
About Zhana
After studying Business Economy in Belgium, Zhana started working for the family business, Termoplast, in Bulgaria from 2009. She initially started as a packaging designer and has since worked in every division of the company from product packer to working closely with the CEO of the company, learning the ropes.
Photo credits: Termoplast
Like this article? Click below to receive the latest articles, Aegg product launches and industry news.