Glass handling on filling lines: a guideline to prevent breakages
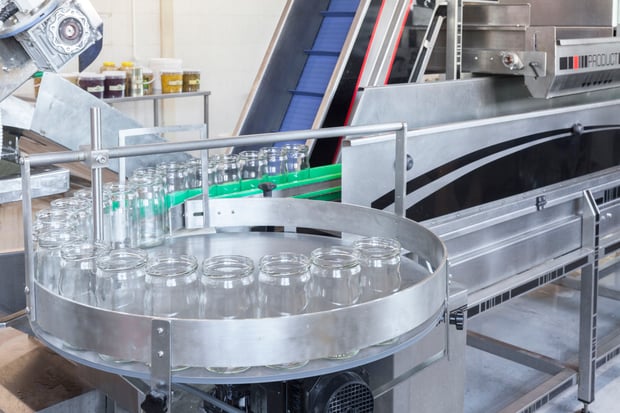
Mark Gaskin, Aegg's Technical Sales Manager for glass packaging gives the lowdown on glass handling on filling lines to prevent breakages...
Many people are aware of the process for glass container production and are familiar with the pallets of glass supplied, but bottles and jars also need to be handled correctly at each stage of their journey through the filling line into their final pack for optimum results.
Glass companies are well aware of the considerations needed when transporting containers along a production line and through to the palletiser to build pallets for transportation to the customer. However, after delivery care is still very important when handling glass to prevent damage and unnecessary breakages.
Effects of Poor Glass Handling
Poor handling can result in difficulties running the line at the optimum speed and reduce efficiencies, as well as causing breakages which results in downtime for cleaning. There is also the loss of containers to consider or, in the case of filled containers, the loss of product as well as containers.
Sometimes line handling difficulties can result in having to employ additional labour to help the line run smoothly and this adversely impacts on productivity. There is also the risk of damaging the container, resulting in immediate breakage or breakage at some later stage in the process, transportation or worse still, with the consumer.
General Glass Handling Guidelines
Conveyor Speeds: It is important when setting the speeds of conveyors to set them to the minimum speed consistent with required production throughput. There is no point in setting conveyors to supply 1000 bottles per minute if you only fill at 500 bottles per minute. The excess speed can result in impact breakage or wear to the stipple when the bottles are stationary.
Avoid drastic changes in speed between conveyors at transfers. If the difference in speeds between one conveyor and the next is more than 15m/s this can cause a bottle to topple, resulting in downware and possible damage to the ring area. Normally this would affect containers prior to the filler more than ones that have been filled, but it will very much depend on the shape of the container.
For the same reasons it is also better to stop and start conveyors gradually. This will help with bottle stability but also help prevent heavy impacts from approaching containers hitting stationary ware.
Deadplates: Ensure that conveyor levels are correct. It is important that bottles travelling down a line do not hit a step-up situation. This can cause bottles to trip resulting in chipped rings or damage the heel area. It can also cause metallic scuffing origins resulting in the bottle failing at a later stage.
Trip Points: Keep clearances between conveyors to a minimum and avoid using dead plates. Gaps between conveyors can lead to trip points resulting in fallen bottles that may cause chipped rings and excess accumulation in roll-out trays.
Metal to Glass Contact: Avoid all bare metal to glass contact, especially in areas of line pressure, as this can cause metallic scuffing as mentioned above. Cover guide rails in nylon/plastic material and ensure there are no screws or bolts sitting proud of the surface. Ensure deadplates are flush or slightly stepped down, including at pasteuriser exits. Ensure conveyor end covers do not encroach into the bottle flow and impinge on the heel and cover the end of lane guides going into the packer.
Container Impacts
The kinetic energy of a single container impacting stationary containers on a line can be measured using the formula K.E= ½MV2.
From this you can see that impact energy increases with the square of the impact speed. Also, that impact increases proportionately to the mass of the container.
For the same impact speed, filled containers suffer much higher impact than empty containers. This will need to be taken into consideration when setting line speeds after the filler.
The mass of the container when empty and filled is normally set by the container and the product, so in most cases it is only possible to influence the speed of the container along the filling line. However, containers on a filling line can often be in contact with each other, particularly on a single line conveyer. Impact of accumulated ware on stationary glass can be high even at low speeds, as the mass of the accumulated containers may be many times that of a single container. For example, if 10 containers are in contact when they hit stationary glass then the mass in the equation above is 10 times that of a single container.
Maximum recommended (empty or filled) impact speeds should not be exceeded. Glass containers have a specified minimum impact strength e.g. 35 inches per second, as measured using an AGR impact tester. This will ensure they convey and fill down the customer’s filling line and during normal handling in trade. Every effort must be made to make sure this value is not exceeded. Otherwise there is the potential for breakage, downtime for line cleaning and possible loss of product.
Line Pressure
This is generated by friction between base of container and the conveyor chain and is only generated when conveyors run faster than the glass.
The amount of line pressure depends on the weight of bottle, the number of bottles in contact in a queue and the coefficient of friction (glass to conveyor).
To help prevent this choose lower friction conveyor chain material and / or use line lubrication. Try to keep mass flow conveyor sections short and stop them as they fill up to prevent one long line of bottles and use `wavy guides’ on single file sections to limit line pressure.
Additional advice can also be found in Tec 9 “General Guidelines for the Use of Glass Containers”
For more information on this article, please get in touch