Glass lightweighting
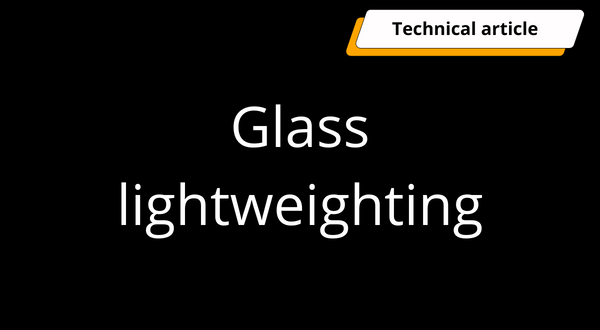
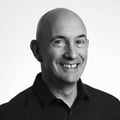
Glass 'lightweighting' or 'rightweighting':
what are they, and what are the considerations?
Mark Gaskin, Aegg's Product Development Manager for glass packaging gives the lowdown...
How did lightweighting come about?
Lightweighting, and more latterly rightweighting, are terms that have been around in the glass industry for a long time. Lightweighting in particular has been around since I first started back in the 80’s when we were lightweighting beer bottles and moving from the heavier blow-blow returnable bottles to lighterweight one-trip NNPB (narrow neck press and blow) bottles.
This change in process, with its ability to give more uniform distribution of glass, enabled container manufacturers to make thinner walled bottles, because they are not compensating for the settle-wave (a “Ghost” area which is seen approximately in the bottom 1/3 of a bottle). This reduced their overall weight and helped reduce the use of raw materials, reduce melting costs (although there are many other production costs to take account of) and helped with transport costs by either reducing fuel costs or increasing load capacity.
Jars and similar wide-mouth containers on the other hand have been made by the Press-Blow process for a very long time. So, without a process change, as with narrow neck bottles, are there other ways we might be able to reduce weight but maintain performance?
Are there other ways to reduce weight but maintain performance?
There are of course refinements to the process that allow a lighter weight to be achieved, and there are many new innovations to improve consistent manufacture and automatic inspection, as many of us would have seen at the Glasstec exhibition in Dusseldorf. But you can’t keep taking weight out, as you need to maintain a minimum glass thickness, and containers needs to perform consistently well. There is no point in making the glass so thin that it constantly breaks on the filling line. Also, from a glass makers point of view, they may have to make an item that runs down a variety of filling lines, from well-controlled high-speed lines with only low impacts, to an old line with high impacts and poor container handling.
Can lightweighting be applied to all glass articles?
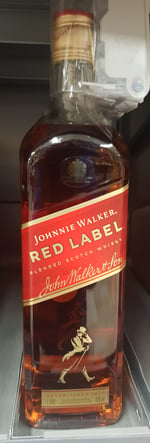
Lightweighting is not an exact science and will vary from container to container.
If you have a non-round or intricate shape, sharp returns on the label panel, engraving, the product is pasteurised or carbonated, these things can influence how much glass a manufacturer is willing to remove.
You may know that larger diameter bottles require thicker glass and returnable bottles are heavier because they accumulate damage during many trips. Bottles with high carbonation may be produced at a returnable weight to ensure they stand up to the internal pressure during processing, pasteurisation and subsequent transport and handling.
Is there a rule of thumb for lightweighting?
When I first started the rule of thumb was that no container should have a weight to volume ratio of less than 0.5 e.g. a 500ml beer bottle, should not be less than 250g, or a 1 lbs Jam Jar less than about 190g, which makes good sense most of the time. However, with cutting edge processes and clever design, incredibly lightweight containers have been produced, with a weight to volume ration down to around 0.4, as with some wine bottles or mayonnaise jars.
These do tend to be uncomplicated, featureless, smooth containers though, so not something that can be easily translated to other products, where, of course, Marketing departments may want to add their own unique touch to the product with engraving and details to make the container stand out on the shelf.
What are the compromises for lightweighting?
So, there is a compromise to be had. Maintaining glass thickness to satisfy the guidelines and specifications, performance consideration of the product and line it is filled on, and marketing considerations like engraving and label panels. Balanced against any savings that may be had reducing the weight.
In the past, lightweighting of some articles may have pushed the boundaries and abilities of the producers, even to the detriment of line performance. So right-weighting was termed as the correction to this, returning bottles to a slightly higher weight, more suitable to the container and conditions it was being used for. Generally, improving the efficiency of manufacture and also providing a more consistent performance on the filling line.
What considerations should be thought of before lightweighting?
There is no magic wand to wave to automatically reduce the weight of any container by, say, 10%. This is a process of discussion with your glass manufacturer, but also a consideration of your own line, product and requirements. Look first at your filling line and check for poor handling, raised deadplates, glass to metal contact, high speed impacts etc. Can these be improved so an already available lightweight container can be used?
Check container dimensions: can they be altered so thinner glass is sufficient? Can the shape of the container be altered to allow a weight reduction e.g. from square to round?
Can the finish be changed to give a slight weight saving? Is engraving required or can the marketing aspects be incorporated in the labelling? Are high carbonation levels necessary? Does pasteurisation of the product need to take place in the bottle or jar, or can this be flash pasteurised and aseptically filled? These are all points that may help with weight reduction.
There are also some products that you may want to remain in a heavier blow-blow bottle to impart a ‘quality’ image e.g. A more expensive whisky or nice wine. Whereas, perhaps with the less expensive end of the market you may want to use lighterweight NNPB whiskies or wines, where some great weight savings can be achieved.
In summary...
I would love to be able to say if you have a particular item, you can reduce the weight by such and such a percentage, but in reality, it is a case of sitting down with your supplier and having a conversation about what they feel may be possible. Then working together to produce an item that suits both parties.
If you are interested in moving to a lighter weight container, then contact the Aegg sales team and start that conversation now.
To read more Aegg technical articles, please click here