Aegg's New Quality Manager Reinforces a Strong Quality Culture
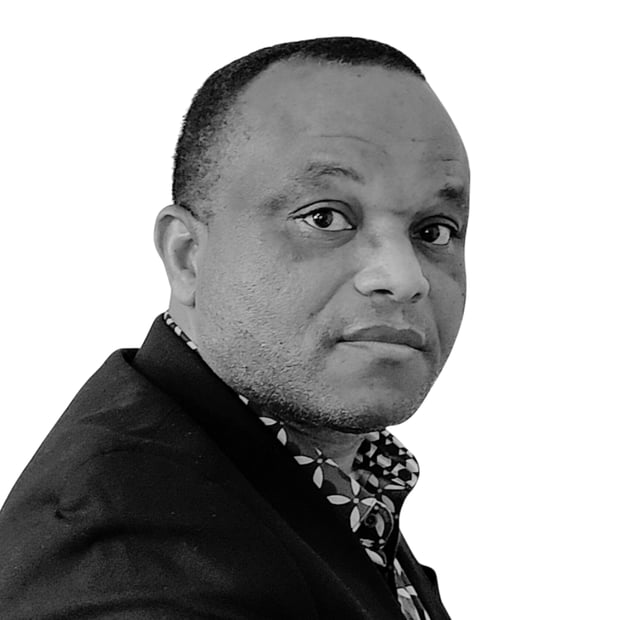
Due to expansion and a large number of new project wins, Aegg Creative Packaging has welcomed a new Quality Manager to the team, Leo Ehigiator, to support the growth of the company through the quality of its products, procedures and culture.
Read Leo's interview to find out how he is supporting Aegg with its quality control…
What does your role at Aegg entail?
The quality of our products is crucial to the success of our business. My role as the Quality Manager is to ensure that Aegg’s products and processes meet quality standards, conform to regulatory requirements, and meet our customers’ specifications through a Robust Quality Management System (QMS).
I liaise with other managers and staff and provide training, tools and techniques to enable others to achieve quality standards. I review existing policies and make suggestions for changes and improvements and how to implement them. I monitor the performance of our suppliers and other third parties by gathering relevant data and product statistical reports. I review customer feedback to understand customer demands and expectations of our products and services. I work with the management team to provide recommendations and solutions to enhance quality.
What are your goals with the job?
There are several personal goals, short and long terms. My immediate goal was to review all policies, procedures and documents, and update where required.
Next, was to complete Aegg BRCGs certification. We had a BRCGs pre-audit assessment and are now in BRC audit preparedness mode for 2025.
My long-term goal is to support Aegg in its vision of continuous growth by continued reinforcement of a strong quality and safety culture- making Aegg the preferred source of packaging, globally.
What is your background and how does this experience help with your role at Aegg?
For over two decades, I worked in in the quality department of a global leading medical diagnostic device manufacturing company, where I was responsible for quality control and assurance. I was involved in FDA preparedness audits, validations, procedures writing, process improvements, lean manufacturing, Kaizen projects, auditing, planning and leading a team of five.
What do you like about working at Aegg?
In my previous work, there were over 600 employees across 3 sites. The team at Aegg is a little smaller creating a very close-knit, friendly, caring and helpful team. It makes it easier to work together towards the same purpose. With the continuous growth of the company, there are great opportunities for the Quality Department to establish the platforms for sustained growth.
I look forward to seeing what the future brings alongside the great team here at Aegg...
To get the latest Aegg packaging news, views and updates, please click here: